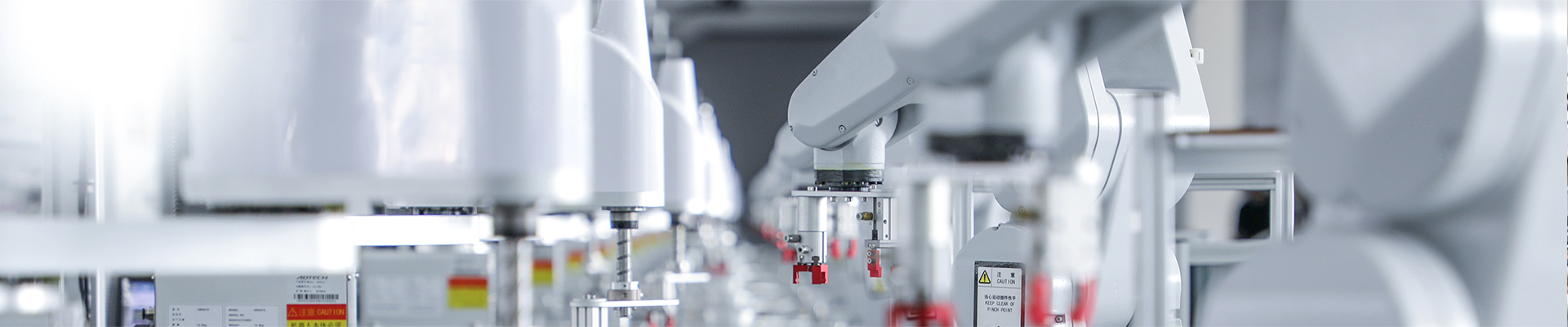
How do specialized cable protection systems and backfill materials contribute to the longevity and reliability of buried cables?
2025-07-19Specialized cable protection systems and carefully selected backfill materials are crucial for safeguarding buried cables against external damage, moisture ingress, and thermal stress, thereby significantly contributing to their longevity and reliability:
-
I. Cable Protection Systems:
-
Conduits/Ducts:
-
Description: PVC, HDPE (High-Density Polyethylene), or concrete conduits encase the cable, providing a primary physical barrier.
-
Benefit: Protects against direct impact, allows for future cable replacement/addition without re-excavation (pulling new cables through existing conduits), and prevents moisture ingress. HDPE is increasingly popular for its flexibility, durability, and long continuous lengths.
-
-
Cable Ties & Spacers:
-
Description: Used within conduits or trenches to maintain proper separation and alignment of multiple cables.
-
Benefit: Prevents cables from rubbing against each other, reduces heat buildup (by allowing airflow), and ensures uniform stress distribution.
-
-
Warning Tapes/Mesh:
-
Description: Brightly colored, detectable tapes or mesh laid above the cable at a specific depth.
-
Benefit: Serves as a visual warning during future excavation, indicating the presence of buried utilities and preventing accidental strikes.
-
-
Duct Seals/End Caps:
-
Description: Used to seal the ends of conduits in manholes, vaults, or at building entries.
-
Benefit: Prevents water, gas, rodents, and debris from entering the conduit, protecting the cable and connected equipment.
-
-
Armored Cables:
-
Description: Cables with an additional layer of steel tape or wire armor under the outer jacket.
-
Benefit: Provides robust protection against crushing, cutting, and rodent damage, especially in direct burial applications or areas with high mechanical stress.
-
-
-
II. Backfill Materials:
-
Thermal Conductivity:
-
Importance: Cables generate heat when energized. The surrounding backfill must efficiently dissipate this heat away from the cable. Poor thermal conductivity leads to overheating, which degrades insulation and reduces cable life.
-
Best Practice: Using "thermal backfill" or "flowable thermal grout" – engineered materials (e.g., sand-cement mixtures, crushed rock fines) with high thermal conductivity that compact well and provide consistent heat dissipation.
-
-
Compaction & Stability:
-
Importance: Proper compaction prevents voids (which can trap moisture or lead to ground settlement) and ensures the cable remains in its designed position. Unstable backfill can allow movement that stresses the cable.
-
Best Practice: Using granular, well-graded materials that compact uniformly, often laid in layers and mechanically compacted. Flowable fills provide excellent compaction around the cable.
-
-
Non-Corrosive Properties:
-
Importance: The backfill material should not be chemically reactive with the cable jacket or other protection systems to prevent long-term degradation.
-
Best Practice: Avoiding highly acidic or alkaline soils, or using neutral backfill materials around the cable zone.
-
-
Absence of Sharp Objects:
-
Importance: The backfill immediately surrounding the cable should be free of rocks, broken glass, or other sharp debris that could puncture or abrade the cable jacket during laying or due to ground movement.
-
Best Practice: Using screened, fine-grained sand or select fill directly around the cable.
-
-
Our company not only manufactures the essential cable pulling and laying equipment but also advises on the best practices for incorporating these vital protection systems and backfill materials, ensuring that your buried cables deliver reliable performance for decades.